Powering Up Panel-Level Packaging! Capcon’s Die Bonder Wins Bulk Adoption by Internationally Leading IDM Giant
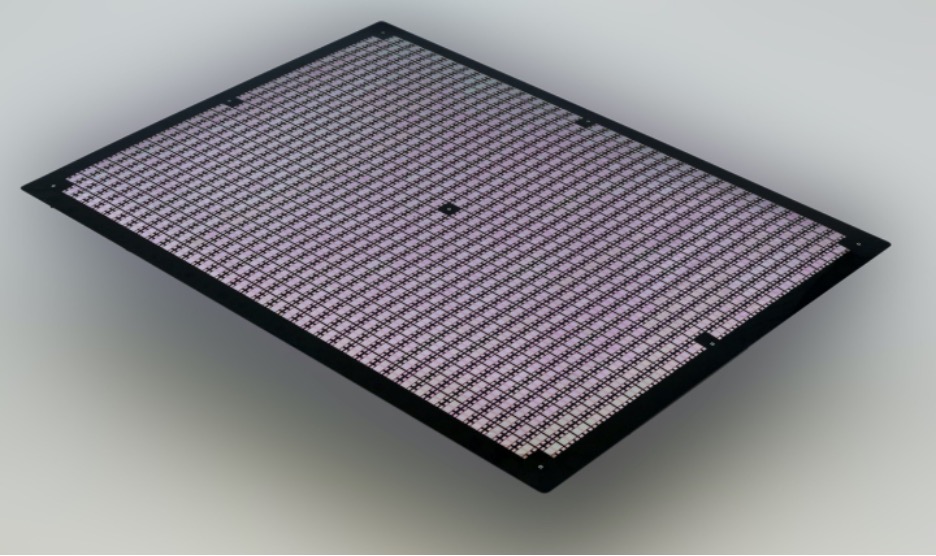
Recently, Capcon’s large panel-level packaging die bonder, AvantGo L6 (Leo), has been adopted in bulk by an Internationally Leading IDM manufacturer and mass producer. It is believed that with the bulk application of AvantGo L6 by client, it will lead the panel-level packaging equipment towards maturity, laying a solid foundation for the development of the panel-level packaging industry and opening a new chapter of advanced packaging with low cost and high efficiency.
As the evolution of Moore’s Law slows down, the semiconductor industry enters the “post-Moore era,” where the importance of advanced packaging becomes increasingly prominent. As an important innovation of Advanced Packaging Technology, panel level packaging has great potential to bring about greater efficiency in manufacturing and cost. It is attracting the attention of industry leading Fabless, OSAT and IDM to position the technology as part of their packaging roadmap and process development.
However, due to the lack of unified standards in the panel-level packaging industry, the panel sizes used by various manufacturers are not the same, and the maturity of the processes is low. The lack of upstream equipment and materials has led to the market still being in the eve of an outbreak, with many technical issues still needing to be addressed.
For example, die bonder is one of the Key equipment. For die bonder, the substrate size used in panel-level packaging is larger, so the surface prone to warping. This requires a larger machine size, a longer Pick & Place action path, higher machine’s efficiency, motion mechanism’s consistency, and stability, which traditional die bonder cannot meet.
In this context, Capcon launched the high-precision die bonder for panel-level packaging- AvantGo L6, based on its own R&D capabilities in electronic control systems, mechanical design, algorithms and other underlying technologies. L6 operates with a dual gantry system offering high UPH up to 12k and accuracy up to +/-5um. It offers unparalleled process flexibility. It comes with capability to handle panel size up to 700*750mmm, face up and face down within the same system; dual wafer handling for multi chip applications. These specifications largely meet the requirements of panel-level packaging for increased substrate size, improving work efficiency, consistency, stability, and accuracy, elevating the capabilities of panel-level packaging to a new level.
It is understood that Capcon’s AvantGo L6 is highly flexible and convertible, covering all processes and sizes, helping customers better adapt to the rapid development in the field of advanced packaging, quickly adjust production capacity across different process with a lower cost.
In the long term, panel-level packaging has a huge application prospect in fields such as Sensors, Power ICs, RF, Link Modules, PMICs, etc. About 66% of chips in automobiles can be produced using fan-out panel-level packaging technology, making it an excellent solution for automotive-grade chip manufacturing.
According to a report by Yole, the GAGR of panel-level packaging is expected to reach 30% over the next five years, with the global output value expected to reach $457 million in 2024. OSATs, IDMs, Foundries, and panel manufacturers have all “sniffed out” the business opportunity, anticipating that panel-level packaging is on the verge of a market explosion.
As a leading supplier of advanced packaging equipment in the industry, Capcon has a bullish long-term outlook of panel-level packaging technology, keeping pace with the development of the advanced packaging. It is focusing on wafer-level packaging equipment, panel-level packaging equipment, and substrate-level packaging equipment, committed to providing customers with advanced semiconductor packaging products, technology, and solutions.
Capcon Singapore Pte. Ltd.
BINGYI ZHANG
www.capconsemicon.sg
Singapore